Como Garantir o Alinhamento de Turbina a Vapor e Evitar Problemas Operacionais
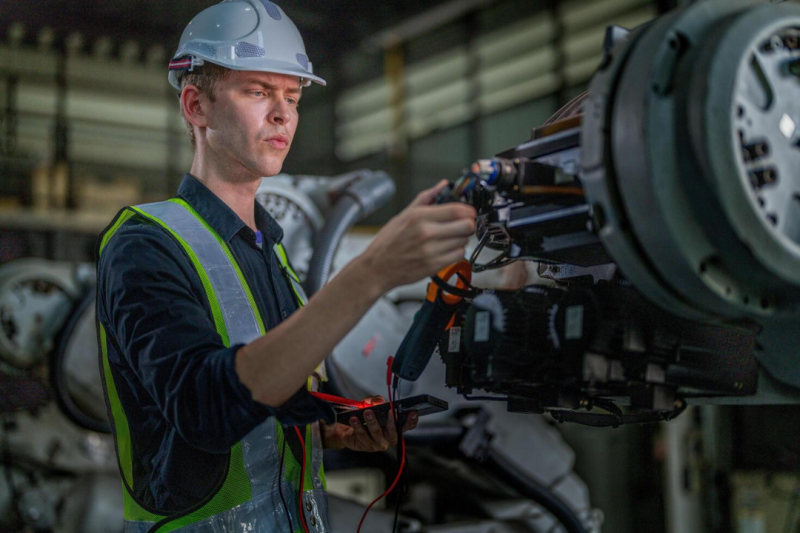
Por: Tiago - 22 de Julho de 2025
O alinhamento de turbina a vapor é um processo essencial para garantir a eficiência operacional em usinas e indústrias. Um correto alinhamento não apenas maximiza o desempenho do equipamento, como também minimiza o desgaste prematuro e os custos com manutenção. Neste contexto, entender as causas do desalinhamento e adotar técnicas adequadas é fundamental para otimizar a operação da turbina.
Importância do Alinhamento de Turbinas a Vapor para a Eficiência
O alinhamento de turbinas a vapor desempenha um papel crucial na eficiência operacional das usinas, pois um sistema alinhado permite uma transferência de energia mais eficiente entre a turbina e os equipamentos conectados.
Quando as turbinas estão devidamente alinhadas, a vibração é reduzida, o que resulta em menor desgaste em componentes mecânicos. Essa redução de vibração evita danos ao rolamento e alivia a carga nos eixos, prolongando a vida útil do equipamento.
Além disso, um bom alinhamento permite que as turbinas operem em condições ideais, mantendo a pressão e a temperatura do vapor constantes. Isso é essencial para garantir que o calor seja utilizado da melhor maneira possível, impactando diretamente na eficiência térmica e no rendimento da planta.
Outra consequência positiva do alinhamento adequado é a redução do consumo de energia. Turbinas desalinhadas podem exigir mais esforço do sistema, levando a um aumento no consumo de vapor e, consequentemente, na conta de operação. Preventivamente, o alinhamento correto minimiza esses desperdícios.
O processo de alinhamento também faz parte de uma estratégia de manutenção preditiva, permitindo identificar problemas potenciais antes que eles causem falhas significativas. Manter as turbinas perfeitamente alinhadas deve ser uma prioridade para qualquer operação que busque eficiência e segurança.
Principais Causas de Desalinhamento em Turbinas a Vapor
O desalinhamento em turbinas a vapor pode ocorrer devido a várias causas, sendo a instalação inadequada uma das mais comuns. Se os suportes ou bases da turbina não forem nivelados corretamente, isso resultará em um desalinhamento inicial que pode se agravar ao longo do tempo.
Mudanças térmicas também são responsáveis por causar desalinhamento. As turbinas e seus componentes, ao operar em temperaturas elevadas, sofrem expansão térmica. Se essa expansão não for considerada durante a instalação, pode levar a deformações e desalinhamento.
Além disso, a vibração excessiva durante a operação, causada por desbalanceamento ou desgaste de componentes, pode contribuir para o desalinhamento. Vibrações contínuas podem comprometer a integridade mecânica dos eixos, levando a uma deterioração acelerada do alinhamento.
Outro fator importante é o desgaste de rolamentos e mancais. Com o tempo, o uso contínuo pode resultar em folgas que afetam negativamente o alinhamento, fazendo com que a turbina não opere conforme projetado. A manutenção regular é essencial para mitigar esse problema.
Por fim, choques mecânicos ou eventos inesperados, como falhas elétricas ou quedas de pressão, podem resultar em desalinhamento súbito e grave. Esses eventos devem ser monitorados de perto, pois podem levar a danos catastróficos se não forem tratados prontamente.
Técnicas de Alinhamento de Turbinas: Métodos e Equipamentos
As técnicas de alinhamento de turbinas a vapor são fundamentais para garantir a eficiência e a longevidade do equipamento.
Diversos métodos e ferramentas podem ser utilizados para realizar o alinhamento com precisão.
Uma das técnicas mais comuns é o alinhamento por laser, que utiliza feixes de luz para medir a posição relativa dos eixos.
Este método é altamente preciso e permite ajustes em tempo real, tornando-o ideal para operações industriais que exigem alta confiabilidade.
Outra abordagem é o alinhamento com medidores de precisão mecânicos, que utilizam indicadores de comparação para verificar o alinhamento de eixos.
Embora menos tecnológica, esta técnica ainda é amplamente utilizada, especialmente em locais que carecem de equipamentos mais avançados.
As ferramentas de alinhamento também são essenciais nesse processo.
Equipamentos como níveis, alinhadores a laser e até mesmo aplicativos móveis são frequentemente utilizados para facilitar o processo de medição e correção de alinhamento.
Além disso, a utilização de softwares de análise pode potencializar o processo de alinhamento.
Esses programas analisam os dados coletados durante a medição e oferecem recomendações para ajustes, tornando o processo ainda mais eficiente e preciso.
Independentemente do método ou equipamento escolhido, é importante seguir um procedimento rigoroso de alinhamento, que inclui a verificação inicial, ajustes necessários, e testes de repetibilidade para garantir que o alinhamento foi realizado com sucesso.
Impactos do Desalinhamento na Durabilidade da Turbina a Vapor
O desalinhamento em turbinas a vapor pode ter impactos significativos na durabilidade do equipamento. Quando uma turbina não está alinhada corretamente, pode ocorrer aumento da carga mecânica em componentes críticos, como eixos e rolamentos.
Esse aumento de carga leva ao desgaste prematuro dessas peças, resultando em falhas mecânicas mais frequentes. Rolamentos desalinhados, por exemplo, podem superaquecê-los, o que prejudica a lubrificação e acelera o processo de deterioração.
Adicionalmente, o desalinhamento aumenta a vibração do sistema. Vibrações excessivas não apenas provocam desconforto sonoro, mas também podem causar danos a outras partes da turbina, levando a avarias em sistemas adjacentes, como tubulações e suportes.
Outro efeito direto do desalinhamento é a diminuição da eficiência operacional. Turbinas desalinhadas não conseguem converter energia térmica em energia mecânica de maneira eficaz, resultando em perda de desempenho e aumento dos custos operacionais devido ao consumo excessivo de vapor.
Em implementação a longo prazo, todos esses fatores contribuem para uma redução significativa na vida útil da turbina. Portanto, adotar práticas regulares de alinhamento e manutenção é vital para prevenir esses problemas e garantir a operação eficiente da turbina a vapor.
Fases de Inspeção e Manutenção para Alinhamento de Turbinas
A inspeção e manutenção de turbinas a vapor são essenciais para garantir seu alinhamento adequado e o funcionamento eficiente.
O processo pode ser dividido em várias fases, cada uma com sua importância específica.
A primeira fase envolve a inspeção visual.
É fundamental verificar a condição dos suportes, das bases e dos componentes externos da turbina.
Procurar por sinais de desgaste, corrosão ou danos visíveis pode ajudar a identificar problemas que podem afetar o alinhamento.
A segunda fase é a verificação das especificações do fabricante.
É importante consultar a documentação técnica para entender as tolerâncias e os requisitos do alinhamento, assegurando que todos os parâmetros estejam dentro das normas estabelecidas.
Seguindo, a terceira fase consiste na medição de alinhamento.
Essa etapa pode ser realizada utilizando equipamentos como alinhar a laser ou medidores mecânicos.
As medições devem ser registradas cuidadosamente para comparação e análise.
A quarta fase envolve a análise dos dados coletados durante a medição.
É necessário avaliar se os resultados estão dentro dos limites permitidos.
Se as medições indicarem desalinhamento, ajustes devem ser realizados imediatamente.
Por fim, a quinta fase é a manutenção preventiva.
Aqui, recomenda-se programar manutenções regulares que incluam inspeções periódicas e alinhamentos de rotina.
Este planejamento garante que a turbina opere de forma otimizada e ajuda a evitar problemas futuros.
Desafios e Soluções Comuns no Alinhamento de Turbinas a Vapor
O alinhamento de turbinas a vapor pode apresentar diversos desafios, que podem impactar a eficiência e a durabilidade do equipamento. Identificar e solucionar esses problemas é fundamental para manter o funcionamento adequado da turbina.
Um dos principais desafios é a mudança de temperatura e expansão térmica dos componentes. À medida que a turbina opera, as variações térmicas podem causar dilatações que desestabilizam o alinhamento. Uma solução prática é realizar o alinhamento quando a turbina estiver em condições de operação normal e documentar essas mudanças para referência futura.
Outro desafio frequente é o acúmulo de vibração. Vibrações excessivas podem ser causadas por desbalanceamento ou falhas mecânicas e impactam diretamente o alinhamento da turbina. A solução envolve a adequação do balanceamento dinâmico e a revisão de componentes que possam estar causando anomalias.
As condições ambientais, como umidade e temperatura, também são desafios importantes. Eles podem afetar o desempenho dos equipamentos de alinhamento e do próprio motor da turbina. A recomendação é utilizar equipamentos com classificação ambiental adequada e garantir que a área de trabalho esteja em condições controladas.
Além disso, a falta de treinamento técnico pode ser um obstáculo. Profissionais sem a devida formação podem não reconhecer sinais de desalinhamento ou podem não aplicar técnicas corretas de alinhamento. Soluções incluem a promoção de cursos e treinamentos para a equipe de manutenção, capacitando-a a lidar com esses desafios com mais eficácia.
Por fim, o uso de ferramentas inadequadas também pode dificultar o processo de alinhamento. É essencial utilizar métodos e equipamentos apropriados, como alinhadores a laser e softwares especializados, para garantir que as medições sejam precisas e confiáveis.
O alinhamento de turbinas a vapor é um fator crítico para a eficiência e a durabilidade do equipamento.
Ao compreender a importância do alinhamento, as principais causas de desalinhamento, as técnicas de alinhamento, e os desafios que podem surgir, os profissionais podem implementar soluções eficazes para manter as turbinas em condições ideais de operação.
Investir em inspeção e manutenção regulares, além de treinar a equipe adequadamente, ajuda a evitar problemas que possam comprometer a performance da turbina.
Assim, garantir o alinhamento adequado não é apenas uma questão técnica, mas também uma prática essencial para otimizar a operação e aumentar a vida útil das turbinas a vapor.