Alinhamento de Redutores Para Máxima Eficiência e Durabilidade
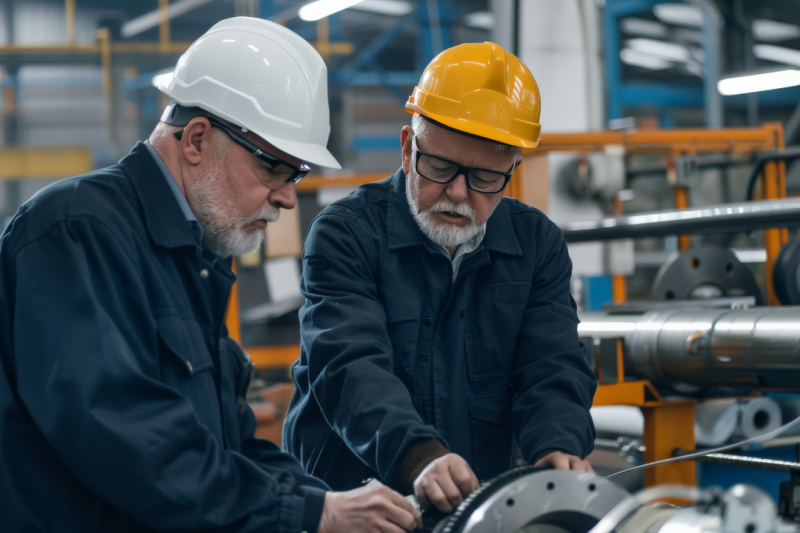
Por: Tiago - 22 de Julho de 2025
O alinhamento de redutores desempenha um papel fundamental na operação eficiente de máquinas e sistemas mecânicos. Um redutor desalinhado pode levar a desgaste prematuro, ruídos excessivos e falhas operacionais, impactando significativamente a performance. Este guia traz informações essenciais sobre as melhores práticas e técnicas para garantir o alinhamento adequado de redutores.
Importância do Alinhamento de Redutores na Indústria
O alinhamento adequado de redutores é crucial para o funcionamento eficiente de equipamentos industriais. Um redutor desalinhado pode resultar em perda de energia, aumento do desgaste das peças e elevação nos custos operacionais.
Na indústria, a operação contínua e confiável das máquinas é vital. Um redutor que não está corretamente alinhado pode causar vibrações excessivas, levando a falhas prematuras nos componentes. Isso não apenas afeta a máquina em questão, mas também pode impactar todo o sistema produtivo, resultando em paradas não planejadas.
Além disso, o alinhamento correto é essencial para maximizar a eficiência energética. Com o redutor alinhado, a transmissão de potência entre o motor e a carga é otimizada, resultando em menor consumo de energia e redução dos custos operacionais. Em um cenário onde a eficiência energética é cada vez mais monitorada, essa prática se torna ainda mais relevante.
Outro aspecto importante é a vida útil dos componentes. O desgaste excessivo causado por desalinhamentos pode levar a um aumento significativo nos gastos com manutenção e reposição de peças. Equipamentos bem alinhados geralmente têm uma vida útil mais longa, contribuindo para uma melhor gestão dos ativos nas empresas.
Por fim, o alinhamento de redutores também é um fator importante para a segurança no ambiente de trabalho. Redutores mal alinhados podem gerar situações de risco, resultando em acidentes que poderiam ser evitados com práticas de manutenção adequadas.
Métodos Comuns para Realizar Alinhamento de Redutores
Existem diversos métodos para realizar o alinhamento de redutores, cada um com suas particularidades e níveis de precisão. Os métodos mais comuns incluem o alinhamento a olho nu, o uso de ferramentas de nível e a aplicação de tecnologias mais avançadas como o alinhamento a laser.
O alinhamento a olho nu é uma técnica básica, porém eficaz para ajustes rápidos. Neste método, o operador observa visualmente o alinhamento das peças e pode fazer pequenos ajustes para corrigir desalinhamentos visíveis. Embora seja uma abordagem simples, ela pode não ser suficiente para aplicações que exigem alta precisão.
O uso de ferramentas de nível, como níveis de bolha ou de laser, é uma maneira mais precisa de realizar o alinhamento. Esses instrumentos ajudam a assegurar que as superfícies dos redutores estejam niveladas, permitindo ajustes mais exatos. Ao alinhar os redutores, o operador pode determinar facilmente quaisquer discrepâncias e corrigi-las.
O alinhamento a laser é considerado o método mais avançado e preciso disponível. Este processo utiliza aparelhos de alinhamento a laser que projetam feixes de luz para determinar o alinhamento exato dos eixos. Este método é altamente confiável e fornece resultados que podem ajudar a evitar problemas de desalinhamento a longo prazo, sendo ideal para aplicações industriais rigorosas.
Além desses métodos, é fundamental seguir boas práticas de manutenção e, em muitos casos, realizar alinhamentos periódicos como parte de um programa de manutenção preventiva. A combinação de técnicas adequadas e ferramentas apropriadas garante a longevidade e a eficiência do equipamento.
Ferramentas Necessárias para Alinhamento Preciso
Para realizar um alinhamento preciso de redutores, é essencial dispor das ferramentas adequadas que garantam a exatidão e a eficácia do processo. As ferramentas necessárias podem variar conforme o método de alinhamento escolhido, mas algumas são consideradas fundamentais.
Uma das ferramentas mais básicas, mas igualmente importantes, é a régua de alinhamento. Esta ferramenta permite medir distâncias e verificar se os eixos estão alinhados. O uso de uma régua ajuda a identificar diferenças de altura entre os redutores, permitindo correções simples.
Os níveis de bolha ou níveis digitais são igualmente importantes, pois ajudam a garantir que as superfícies estejam perfeitamente niveladas. O uso de um nível é fundamental para evitar problemas de desalinhamento causados por ajustes inadequados nas bases dos redutores.
Para quem opta pelo alinhamento a laser, investir em um sistema de alinhamento a laser é essencial. Esses sistemas geralmente incluem um transmissor e um receptor que, conectados por um computador, fornecem dados extremamente precisos sobre o alinhamento dos eixos. Essa tecnologia é especialmente útil em operações que exigem alta precisão e tem se tornado um padrão em diversas indústrias.
Além das ferramentas de alinhamento, é importante ter um conjunto de chaves e ferramentas manuais disponíveis para realizar os ajustes necessários nos redutores. Isso pode incluir chaves de fenda, chaves inglesas e outros utensílios que ajudam na montagem e ajuste dos componentes durante o processo.
Por último, o uso de medidores de vibração pode auxiliar na detecção de problemas posteriores de alinhamento. Esses dispositivos ajudam a monitorar o funcionamento do redutor após a realização do alinhamento, garantindo que esteja operando dentro dos parâmetros aceitáveis.
Sinais de Desalinhamento em Redutores
Identificar os sinais de desalinhamento em redutores é fundamental para prevenir falhas e garantir a eficiência operacional. Existem diversos indicadores que podem sinalizar que um redutor não está devidamente alinhado, e reconhecê-los pode ajudar a evitar danos maiores.
Um dos sinais mais comuns de desalinhamento é a vibração excessiva. Quando um redutor está desalinhado, ele pode causar um movimento irregular que resulta em vibrações anormais. Essa vibração não só pode danificar o redutor em si, mas também outros componentes conectados no sistema, afetando a operação de toda a máquina.
Outro indicador importante é o aumento da temperatura. Um redutor desalinhado gera mais atrito entre as peças móveis, o que pode levar a um aumento significativo da temperatura de operação. Monitorar a temperatura é crucial, pois temperaturas elevadas podem diminuir a vida útil do lubrificante e dos componentes do redutor.
Além disso, um redutor desalinhado pode apresentar ruídos incomuns durante a operação. Esses ruídos podem variar, mas geralmente são descritos como batidas, rangidos ou chiados. Se um redutor começa a produzir sons que não eram audíveis anteriormente, isso pode ser um alerta de desalinhamento.
O desgaste irregular das peças também é um sinal de desalinhamento. Se você notar que as engrenagens, rolamentos ou outros componentes do redutor estão apresentando um desgaste incomum ou desigual, é um indicador de que pode haver desalinhamento. A verificação regular do estado das peças é uma prática recomendada para evitar problemas futuros.
Por fim, a dificuldade no funcionamento do redutor, como lentidão ou falhas ao iniciar, pode ser um indicativo de desalinhamento. Essas dificuldades podem comprometer a operação e causar paradas inesperadas, prejudicando a eficiência do sistema. Portanto, manter um monitoramento constante dos redutores pode ajudar a identificar esses sinais precocemente e garantir a continuidade das operações.
Impactos do Alinhamento Correto na Performance Mecânica
O alinhamento correto de redutores tem um impacto significativo na performance mecânica de sistemas industriais. Quando os redutores estão devidamente alinhados, diversos benefícios podem ser observados, refletindo em eficiência, economia e maior longevidade dos equipamentos.
Um dos principais impactos do alinhamento adequado é a redução do consumo de energia. Com os redutores alinhados, a transmissão de potência entre o motor e a carga é otimizada, o que gera um funcionamento mais eficiente. Isso resulta em menor esforço necessário para mover a carga, reduzindo diretamente os custos operacionais relacionados ao consumo de eletricidade.
Além disso, um alinhamento correto diminui o desgaste das peças. Redutores desalinhados tendem a sofrer mais atrito e pressão em pontos específicos, o que leva a um aumento do desgaste e à necessidade de manutenção frequente. Com o alinhamento adequado, a distribuição de força é mais uniforme, prolongando a vida útil das peças e minimizando a frequência de reparos.
A diminuição das vibrações geradas por um redutor alinhado é outro aspecto importante. Menos vibrações não apenas melhoram o conforto acústico do ambiente industrial, mas também protegem processos sensíveis e equipamentos adjacentes de danos potencialmente graves que podem ser causados por vibrações excessivas.
Um sistema bem alinhado também proporciona melhora na produtividade. Com a eficiência aumentada e menos paradas inesperadas devido a falhas mecânicas, as operações podem ser mantidas em alto desempenho. Isso significa maior produtividade ao longo do tempo, impactando positivamente os resultados financeiros da empresa.
Por fim, o alinhamento correto contribui para a segurança no ambiente de trabalho. Menos falhas mecânicas significam um ambiente mais seguro para os operadores, enquanto a diminuição de vibrações e sons também ajuda a criar um espaço de trabalho mais confortável e livre de riscos.
Manutenção Preventiva e Verificações Periódicas
A manutenção preventiva e as verificações periódicas são fundamentais para garantir o bom funcionamento e a longevidade dos redutores. Implementar um programa de manutenção eficaz permite identificar problemas potenciais antes que se tornem falhas sérias, assegurando assim a continuidade operacional.
Um dos primeiros passos na manutenção preventiva é a inspeção regular dos redutores. Isso inclui uma análise visual em busca de sinais de desgaste, como vazamentos, peças soltas ou danos visíveis. Esses check-ups devem ser realizados em intervalos regulares, conforme a recomendação do fabricante ou baseado na frequência de operação do equipamento.
Além das inspeções visuais, a realização de testes de vibração e análise de temperatura são práticas eficazes para monitorar a condição dos redutores. Através da coleta de dados sobre vibrações e temperaturas, é possível identificar comportamentos anormais que podem indicar desalinhamento ou desgaste excessivo nas peças. Muitas vezes, essas medições podem evitar paradas inesperadas.
Outro elemento importante da manutenção preventiva é a lubrificação dos componentes. A aplicação regular de lubrificantes nas partes móveis é essencial para reduzir o atrito e o desgaste. A frequência e o tipo de lubrificante devem estar de acordo com as especificações do fabricante e com as condições de operação do redutor.
A programação de alinhamentos periódicos também deve estar incluída no plano de manutenção. Mesmo após um alinhamento inicial, os redutores podem sofrer mudanças devido a variações térmicas, vibrações e outras condições operacionais, exigindo verificações regulares para garantir que permaneçam alinhados. Isso pode ser feito com as ferramentas apropriadas, como níveis e sistemas de alinhamento a laser.
Por fim, registrar todas as atividades de manutenção e inspeções é crucial. Esses registros não apenas ajudam a identificar padrões de problemas que possam surgir, como também são valiosos para auditorias e para garantir que estejam seguindo as diretrizes de conformidade. Um histórico bem documentado pode ser um diferencial na gestão de ativos de uma empresa, permitindo melhorias contínuas no desempenho operacional.
Em resumo, o alinhamento de redutores é uma prática essencial para garantir a eficiência e a durabilidade dos sistemas mecânicos. Identificar os sinais de desalinhamento e realizar manutenções preventivas regulares são passos cruciais para evitar falhas e prolongar a vida útil dos equipamentos.
Os métodos utilizados para alinhar redutores, bem como as ferramentas necessárias, desempenham um papel fundamental no sucesso dessa prática. A implementação de técnicas adequadas e a realização de verificações periódicas asseguram que os redutores operem nas condições ideais, promovendo não apenas a performance mecânica, mas também a segurança e a eficiência energética.
Com um sistema de manutenção eficiente e a atenção aos detalhes durante o alinhamento, as indústrias podem melhorar significativamente sua produtividade, reduzir custos operacionais e criar um ambiente de trabalho mais seguro para todos os profissionais envolvidos. Investir no alinhamento correto e na manutenção preventiva dos redutores é, portanto, um passo estratégico para o sucesso operacional.