Alinhamento de Eixos de Turbinas Garantindo Performance Ideal
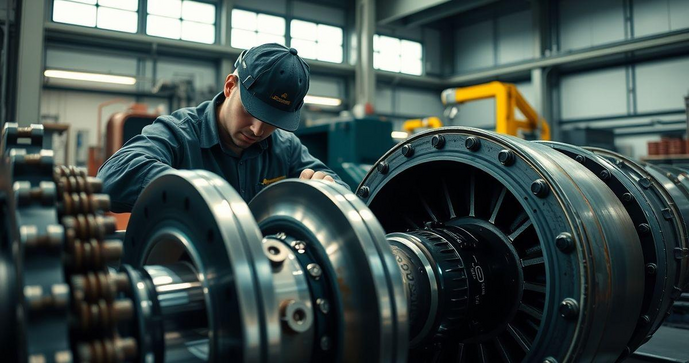
Por: Tiago - 22 de Julho de 2025
O que é Alinhamento de Eixos de Turbinas
O alinhamento de eixos de turbinas é um processo que visa garantir que os eixos de duas ou mais máquinas rotativas estejam em perfeita linha entre si. Este alinhamento é fundamental para minimizar o desgaste, reduzir as vibrações e maximizar a eficiência do sistema de transmissão de potência. Quando os eixos não estão alinhados corretamente, podem ocorrer desgastes prematuros, falhas em componentes e até mesmo paradas inesperadas dos equipamentos.
As turbinas, que são utilizadas em diversos setores como geração de energia e fabricação de produtos, dependem de um alinhamento preciso para operar de forma ideal. O desalinhamento pode levar a problemas significativos, incluindo aumento do consumo de energia, diminuição da vida útil da máquina e necessidade de manutenções mais frequentes. Por isso, entender o que constitui o alinhamento de eixos é essencial para qualquer operação que utilize turbinas.
Existem diferentes tipos de alinhamento, incluindo o alinhamento a laser e o alinhamento com instrumentos mecânicos. Cada método tem suas vantagens e aplicações específicas, mas todos devem ter como objetivo principal a correção de desvios angulares ou paralelogramas.
Importância do Alinhamento Preciso
A importância do alinhamento preciso de eixos de turbinas não pode ser subestimada. Alinhamentos corretos garantem que as forças de operação sejam distribuídas de maneira uniforme, reduzindo assim o desgaste em componentes críticos e otimizando o desempenho operacional. Quando o alinhamento não é preciso, a turbina pode enfrentar vibrações excessivas e cargas desiguais, que podem resultar em falhas catastróficas ao longo do tempo.
Um alinhamento adequado contribui diretamente para a eficiência energética. Turbinas desalinhadas podem exigir mais energia para operar, levando a um aumento nos custos operacionais. Com uma configuração alinhada, as máquinas funcionam de maneira mais suave e eficiente, resultando em economias significativas ao longo do tempo e menor impacto ambiental.
Além disso, o alinhamento preciso ajuda a prolongar a vida útil dos equipamentos. Máquinas que operam em condições ideais têm um desgaste menor, reduzindo a necessidade de reparos e substituições dispendiosas. Isso é especialmente relevante em indústrias onde a continuidade operacional é crucial, como na geração de energia, onde a inatividade pode ter consequências financeiras graves.
Por fim, um alinhamento adequado contribui para a segurança operacional. Equipamentos desalinhados podem falhar subitamente, colocando em risco não apenas a integridade das máquinas, mas também a segurança dos operadores e outros colaboradores. Portanto, investir tempo e recursos em um alinhamento preciso é um passo fundamental para assegurar um ambiente de trabalho seguro e eficiente.
Métodos de Alinhamento de Eixos
Os métodos de alinhamento de eixos são técnicas utilizadas para garantir que os eixos das turbinas estejam alinhados corretamente. Existem várias abordagens, cada uma com suas características, vantagens e desvantagens. A seguir, abordaremos os métodos mais comuns de alinhamento de eixos:
1. Alinhamento a Laser: Este é um dos métodos mais modernos e precisos disponíveis, utilizando feixes de laser para medir o alinhamento dos eixos. A tecnologia a laser permite uma leitura altamente precisa e rápida, o que resulta em correções mais eficazes. Além disso, o alinhamento a laser é ideal para aplicações onde a precisão é crítica.
2. Alinhamento Mecânico: Esse método tradicional é realizado utilizando instrumentos mecânicos, como alinhadores de coluna de dial ou ferramentas de alinhamento em linha. Embora seja menos preciso que o alinhamento a laser, é uma opção viável, especialmente em ambientes onde a tecnologia a laser não está disponível. Esse método requer mais tempo e habilidade do operador para realizar as medições corretamente.
3. Alinhamento com Instrumentos Ópticos: Este método utiliza dispositivos ópticos, como níveis e teodolitos, para medir ângulos e alinhamentos de eixo. É mais comum em grandes turbinas onde o acesso é limitado. Embora não seja tão comum quanto os métodos a laser, ainda é usado em alguns processos industriais.
4. Alinhamento por Análise de Vibração: Este método envolve medir as vibrações da máquina em operação para identificar desalinhamentos. Com a análise de vibração, os técnicos podem diagnosticar problemas em tempo real e prever a necessidade de alinhamento antes que falhas ocorram. Essa abordagem pode ser integrada a programas de manutenção preditiva.
Cada método tem suas aplicações ideais e pode ser escolhido com base nas necessidades específicas da operação. A escolha do método de alinhamento adequado garantirá que as turbinas funcionem de forma eficiente e com um desgaste reduzido.
Impactos do Desalinhamento nas Turbinas
O desalinhamento de eixos nas turbinas pode causar impactos significativos no desempenho e na durabilidade do equipamento. Existem várias consequências negativas associadas ao desalinhamento, que podem afetar tanto a eficiência operacional quanto a segurança do processo.
1. Aumento do Desgaste: Quando os eixos estão desalinhados, as forças de operação não são distribuídas uniformemente, resultando em tensões excessivas em componentes específicos. Isso pode levar a um desgaste acelerado de rolamentos, engrenagens e outros elementos críticos. Pontos de contato inadequados aumentam o risco de falhas prematuras.
2. Maior Consumo de Energia: Turbinas desalinhadas exigem mais força para operar, resultando em um aumento do consumo energético. Isso não somente eleva os custos operacionais, mas também contribui para um desperdício de recursos energéticos, impactando negativamente o meio ambiente.
3. Vibrações Excessivas: O desalinhamento provoca vibrações que podem ser prejudiciais à integridade estrutural da turbina e de seus componentes. Vibrações excessivas podem causar ruídos incômodos e afetar a performance de equipamentos vizinhos, além de aumentar o desgaste dos fixadores e suportes.
4. Redução da Vida Útil: O estresse adicional criado por um alinhamento incorreto pode encurtar significativamente a vida útil da turbina e dos sistemas associados. Isso geralmente resulta em um aumento na frequência de manutenções e substituições de peças, elevando os custos operacionais à medida que os componentes se tornam menos confiáveis.
5. Risco de Falhas Catastróficas: Em casos extremos, o desalinhamento pode levar a falhas catastróficas do equipamento. Isso não apenas resulta em prejuízos financeiros elevados, mas também pode colocar em risco a segurança dos operadores e do ambiente ao redor.
Portanto, a detecção e correção do desalinhamento é essencial para garantir a eficiência, a segurança e a durabilidade das turbinas. Medidas preventivas e manutenções regulares podem ajudar a evitar muitas dessas consequências, assegurando operações mais suaves e confiáveis.
Ferramentas Utilizadas para Alinhamento de Eixos
O processo de alinhamento de eixos de turbinas requer o uso de ferramentas específicas para garantir que as medições sejam precisas e as correções eficazes. Abaixo estão algumas das principais ferramentas utilizadas para esse propósito:
1. Medidores a Laser: Esta ferramenta utiliza tecnologia a laser para realizar medições de alinhamento com alta precisão. O uso de medidores a laser é ideal para identificar desvios angulares e paralelogramas de forma rápida e eficaz. Eles oferecem uma leitura digital fácil de interpretar, reduzindo o tempo de alinhamento.
2. Alinhadores de Coluna de Dial: Uma das ferramentas mecânicas tradicionais, os alinhadores de coluna de dial utilizam instrumentos de leitura para medir o desalinhamento durante a instalação. Embora exijam mais tempo e habilidade do operador, são eficazes em diversas situações.
3. Níveis Ópticos: Os níveis ópticos são utilizados para garantir que as superfícies estejam alinhadas em um plano horizontal ou vertical. Esses dispositivos são importantes, especialmente quando se lida com grandes turbinas em ambientes onde o acesso é restrito.
4. Ferramentas de Análise de Vibração: Equipamentos especializados em análise de vibração são utilizados para monitorar o desempenho da turbina ao longo do tempo. Eles permitem detectar variações que possam indicar desalinhamento, ajudando na implementação de medidas corretivas antes que ocorra um grande problema.
5. Software de Alinhamento: Softwares especializados para alinhamento de eixos são cada vez mais utilizados. Esses programas fornecem visualizações em 3D e relatórios detalhados que ajudam a identificar e corrigir problemas de alinhamento, oferecendo um suporte importante para os operadores e engenheiros.
A escolha das ferramentas apropriadas depende das condições específicas do local, do tipo de turbina e da complexidade do sistema. Investir em ferramentas de alta qualidade pode resultar em um alinhamento mais preciso, reduzindo custos e prolongando a vida útil da turbina.
Boas Práticas na Manutenção de Alinhamento
Manter um alinhamento adequado de eixos de turbinas é essencial para garantir a eficiência operacional e a durabilidade dos equipamentos.
1. Realização de Inspeções Regulares: A realização de inspeções periódicas é fundamental para identificar qualquer sinal de desalinhamento antes que se torne um problema sério. Essas inspeções devem incluir a verificação de componentes críticos, vibrações e relatórios de desempenho.
2. Utilização de Ferramentas Apropriadas: Investir em ferramentas de alinhamento de alta qualidade, como medidores a laser e software especializado, é crucial para garantir medições precisas. Ferramentas adequadas facilitam a correção e o monitoramento do alinhamento ao longo do tempo.
3. Análise de Vibrações: Implementar um programa de monitoramento contínuo de vibrações pode ajudar a identificar problemas de alinhamento rapidamente. A análise de vibrações fornece dados valiosos sobre o desempenho das turbinas, ajudando a antecipar falhas.
4. Documentação Detalhada: Manter registros detalhados de todas as atividades de alinhamento, incluindo medições, correções realizadas e datas de manutenção, é essencial. Essa documentação não só ajuda a rastrear o histórico do equipamento, mas também facilita a identificação de padrões ou recorrências em problemas.
5. Formação e Capacitação de Equipes: Garantir que a equipe envolvida na operação e manutenção das turbinas receba treinamento adequado é vital. O conhecimento sobre os métodos de alinhamento e o uso correto das ferramentas proporciona maior eficiência e segurança durante o trabalho.
6. Reavaliações Periódicas: Implementar reavaliações periódicas das condições de operação pode ajudar a determinar se as configurações de alinhamento ainda são adequadas, especialmente após mudanças significativas nos processos ou após eventos que possam impactar a operação da turbina.
Adotar essas boas práticas garantirá que o alinhamento de eixos de turbinas seja mantido com a precisão necessária, otimizando o desempenho e prolongando a vida útil do equipamento. A manutenção proativa ajudará a evitar falhas significativas e dispendiosas no futuro.
O alinhamento de eixos de turbinas é um aspecto crucial para a eficiência e a durabilidade dos sistemas rotativos. Compreender a importância do alinhamento preciso, conhecer os métodos disponíveis e utilizar as ferramentas apropriadas são passos fundamentais para garantir operações eficientes.
Além disso, a adoção de boas práticas na manutenção de alinhamento não apenas previne problemas, mas também assegura um ambiente de trabalho seguro e econômico. Investir em métodos adequados de alinhamento e na capacitação das equipes é fundamental para maximizar o rendimento das turbinas e minimizar os custos operacionais a longo prazo.